Capacity is at the base of the majority of problems software development companies have to face. This comes as no surprise - the availability of specialists is usually the key to profits.
Unfortunately, it is also a source of numerous challenges, such as:
- allocation of resources,
- swelling benches,
- flexible availability of employees,
- dynamically changing environment,
- high turnover rates,
- difficulties with acquiring new employees.
As a result, capacity has an enormous impact on the condition of the entire company.
That is the reason you should ask yourself: How to plan and manage capacity to improve your operations?
Key takeways: capacity management
With our comprehensive guide, you’ll learn:
- what is capacity management (and, more importantly, what it is not),
- what is the difference between total capacity and available capacity,
- how to calculate resource capacity for different scenarios and situations,
- what conclusions can be drawn from capacity management process,
- what are the best and the worst practices in the field,
- how can your company benefit from business capacity management - and what it is losing without it.
As a result, after reading this article you will be able to:
- define different types of capacity and use them to your company’s advantage,
- choose the right operations management strategy for your business,
- use the general principles of capacity modeling to gain a better understanding of your company’s operations,
- calculate available capacity for specialists with different contracts, hours and planned absences.
What is capacity?
In short, capacity is a maximum production output a company can sustain in its production processes or services. It can be calculated for the entire business, for teams, or even for particular specialists.
In the case of the IT industry, capacity usually refers to the number of available person-hours in a given period of time including all kinds of public holidays.
The capacity can be calculated differently depending on the holidays, absences and other factors impacting the schedules.
This is, however, a complex task we discussed in our guide to capacity for operations management.
Importantly, capacity is also crucial for resource planning in project management and it should not be disregarded!
Types of capacity
Even though the definition of capacity may seem simple, the concept has been divided into a few categories to respond to different business purposes.
As a result, three different kinds of capacity are used to reflect the current situation of the company. Those include:
- total capacity - the number of working hours in the month, week or a day, without any deductions from holidays, leaves and other absences.
- available capacity - total capacity minus absences, public holidays and time scheduled in other projects and tasks.
- billable capacity - total hours of billable time compared to employee’s capacity, or the number of hours they're available to work.
Capacity in IT services - why is it so challenging?
Hardly a day goes by without capacity being mentioned in every digital agency there is. Why?
Because IT service companies profit from selling their employees’ time - and that time is directly reflected in their capacity - I bet that it is a no brainer for you.
For this model of work to be profitable, IT companies need to keep a close eye on numerous issues at once. Those include:
- a wide scope of IT services,
- availability of employees, incl. holidays, maternity leaves and other absences,
- tentative projects and other future opportunities,
- employees’ specializations, skills and ambitions,
- costs of work, incl. types of employment, wages and salaries,
- changes in demand; trends and threats on the market,
- pauses in project, canceled operations and benched employees,
…and many more other issues specific for different companies.
As a result of this complexity, IT companies have to combine many different threads to gain a bigger picture of what’s to come. Of course, they cannot do that in a single spreadsheet. So, the questions are:
- how to manage capacity to do it right?
- how to make capacity reflect the real world accurately?
- how to use capacity to maximize the revenue?
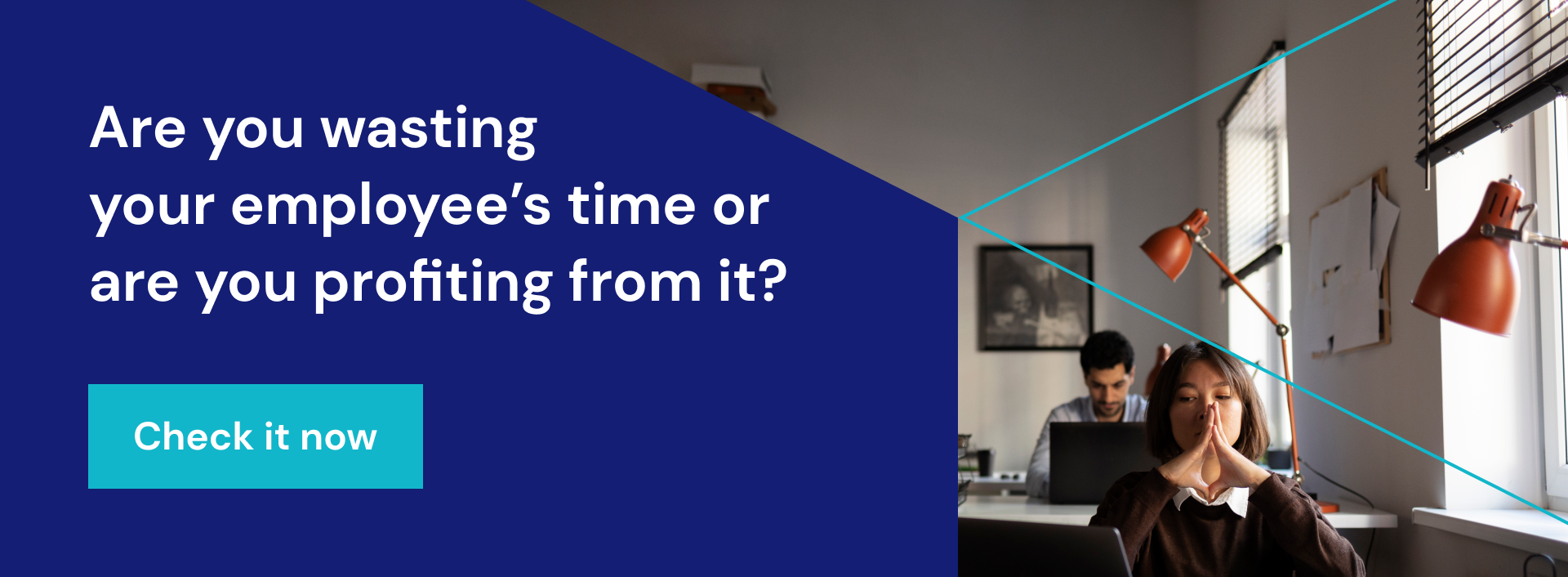
Planning and management for capacity - definition
The definition of capacity planning, also known as capacity management, consists of all types of activities aiming to maximize the company’s output.
In other words, it ensures that a company produces as many products and services as possible.
What is the point of capacity management?
In short, the point of business capacity management is to ensure that the company has enough available resources to complete orders or projects on time and fulfill the business needs of the company.
In an ideal situation, those resources are used to the fullest, without any overtimes or benched specialists.
However, the list of benefits of combining service management with capacity does not end there.
Managers from different industries also value the process of efficient capacity management for:
- the transparency of all the data that allows them to make right decisions,
- the reduction of stock-outs, idle specialists and unexpected delays,
- increased delivery capacity improved by maximizing the number of hours worked,
- identifying inefficiencies in various processes, as well as potential benched specialists in the future,
- providing them with information on their employees’ skills, needs and ambitions, as well as the needs for hiring new specialists.
Types of business capacity managements
Capacity management process consists of 3 types of activities you need to consider to improve your company’s effectiveness. Those include:
- Product capacity management ensures that your business has products, materials necessary for a particular project or service. In the IT industry, this type of planning usually involves analyzing available devices and general know-how.
- Workforce capacity planning is meant to determine the number of hours and, as a result, the number of team members required to complete the process. It starts with analyzing the availability of specialists and their skills that may be used for a particular project. At this point, the company should also consider holidays, absences and other events that may impact the operations.
- Tool capacity planning is included in the equation to make sure that the company has sufficient tools and software to complete the project. Should such a need arise, this type of capacity management can also determine what additional resources are to be bought for a particular purpose.
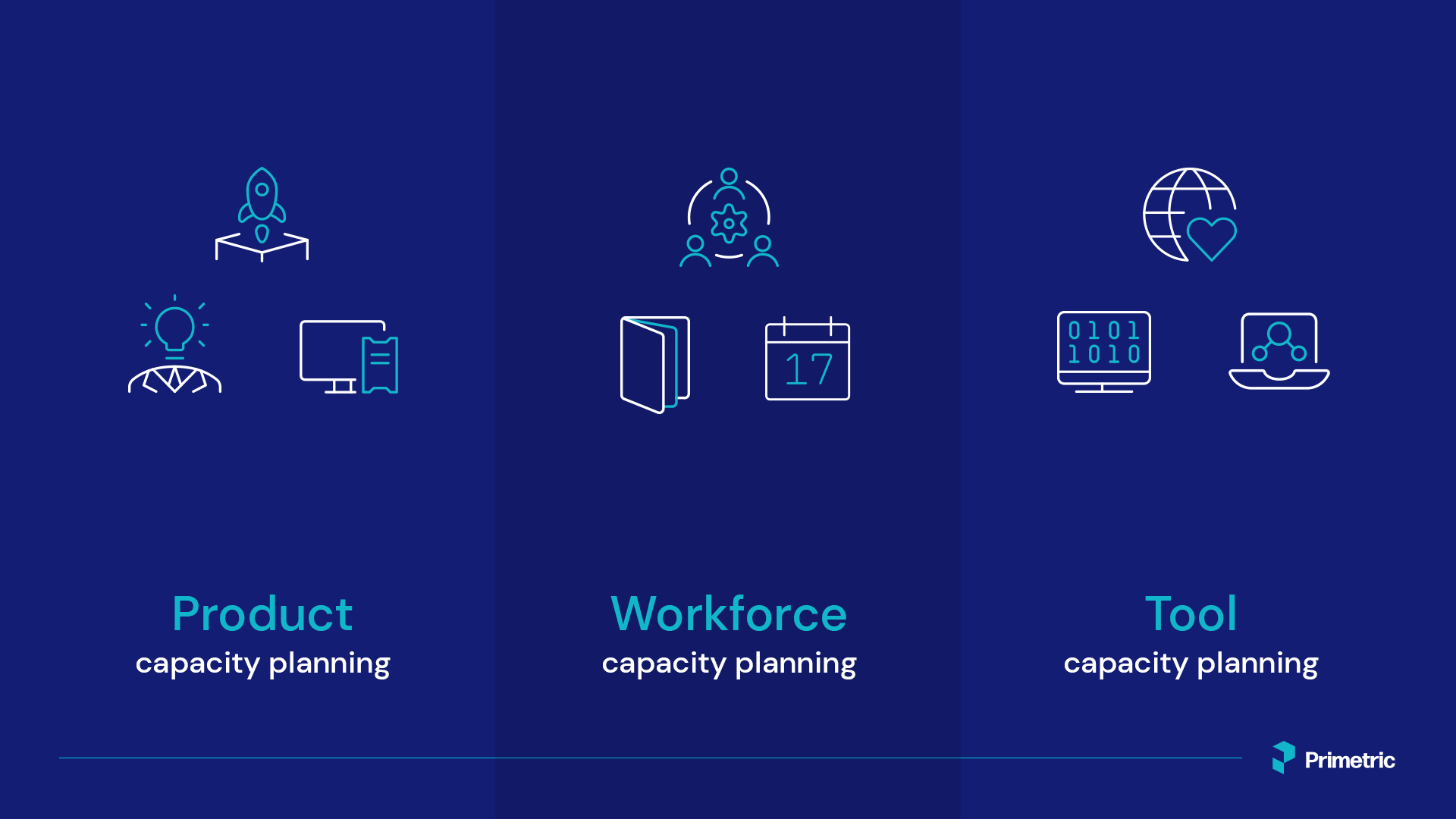
Importantly, those types of capacity management are not to be used separately! To get a detailed overview of what’s to come, they should be combined - not used interchangeably.
However, in the age of outsourcing and the overwhelming number of services, the majority of companies tend to pay close attention to workforce capacity planning. This is especially true for project companies which rely on specialists to generate profit. Therefore, if you want to offer some services to your clients, you should focus on this part of business capacity management.
Capacity and resource planning - what’s the difference?
In some cases, the terms capacity planning and resource planning are used interchangeably - and wrongfully so. In fact, any company needs both of those types of planning to succeed.
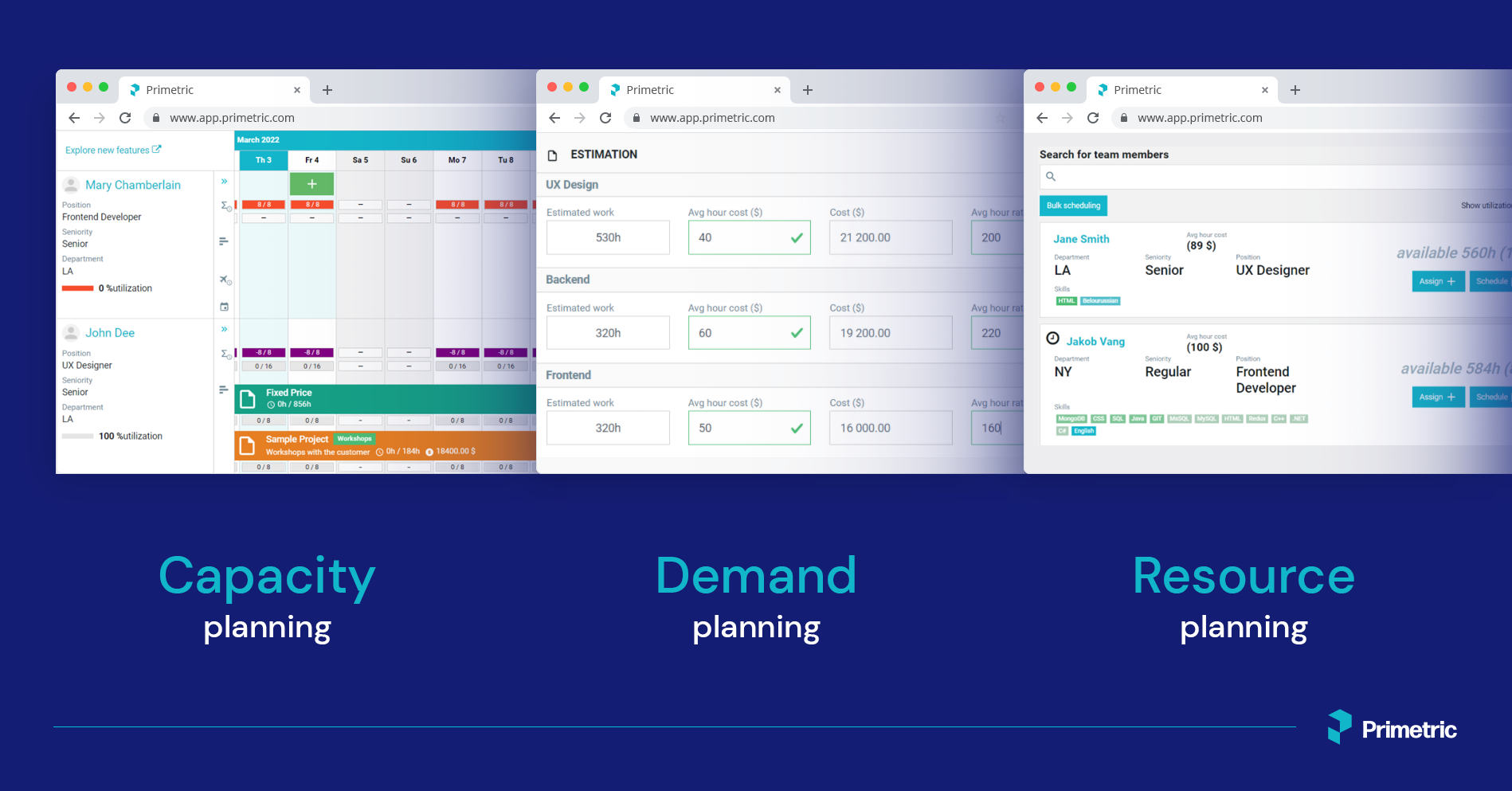
Capacity planning usually is the first step of resource planning. Its aim is to determine whether or not the company has available resources to complete new projects and tasks. As a result, it provides managers with a general overview of a company's abilities.
Further on, companies also have to take into account the process of demand planning. It consists of supply chain management that aims to forecast and predict future needs for resources. In the IT industry, the process usually focuses on demand on human resources, i.e. specialists with particular skills, or their full-time equivalents. In other words, demand planning determines whether the company has the right people to succeed.
Resource planning, on the other hand, uses the information provided by capacity and demand planning on a more specific level to allocate different employees. Therefore, it represents a more detailed and practical approach.
Note: capacity management process is the most effective when combined with both resource planning and demand planning!
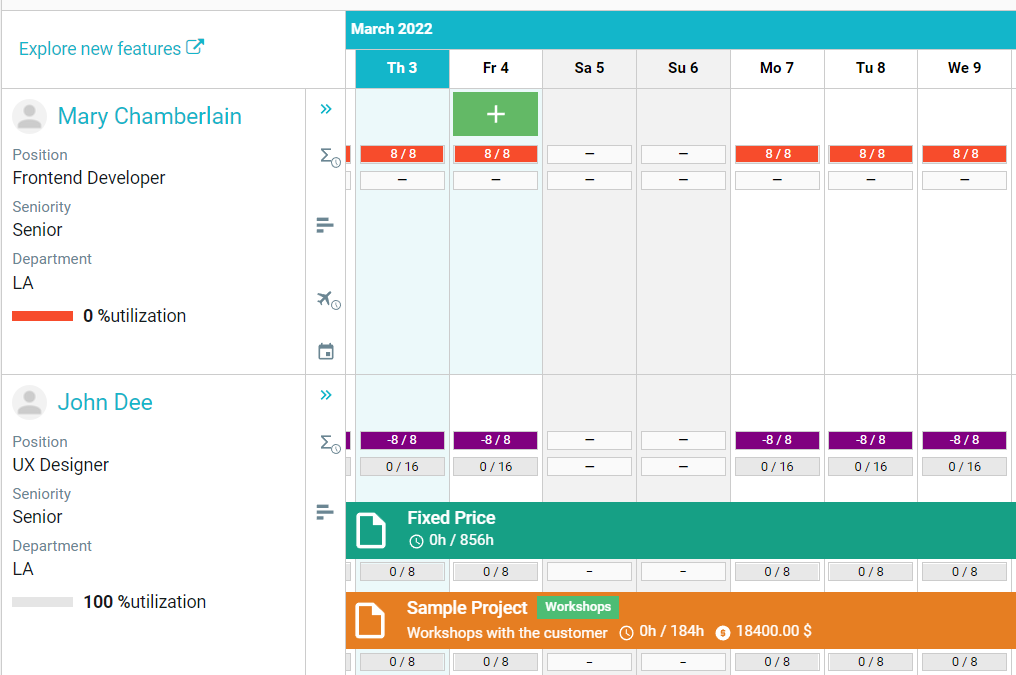
Capacity management plan displayed in Primetric:
- red lines - available capacity with no allocations
- purple lines - planned capacity
- gray lines - tracked hours: total (field at the top of the employee’s bar) and divided into projects (gray bars below allocations)
Demand planning:

During the demand planning phase, the project is divided into consecutive phases. Capacity managers, analysts and other people involved then decide what amount of work is needed to complete each phase of the project.
Resource planning:
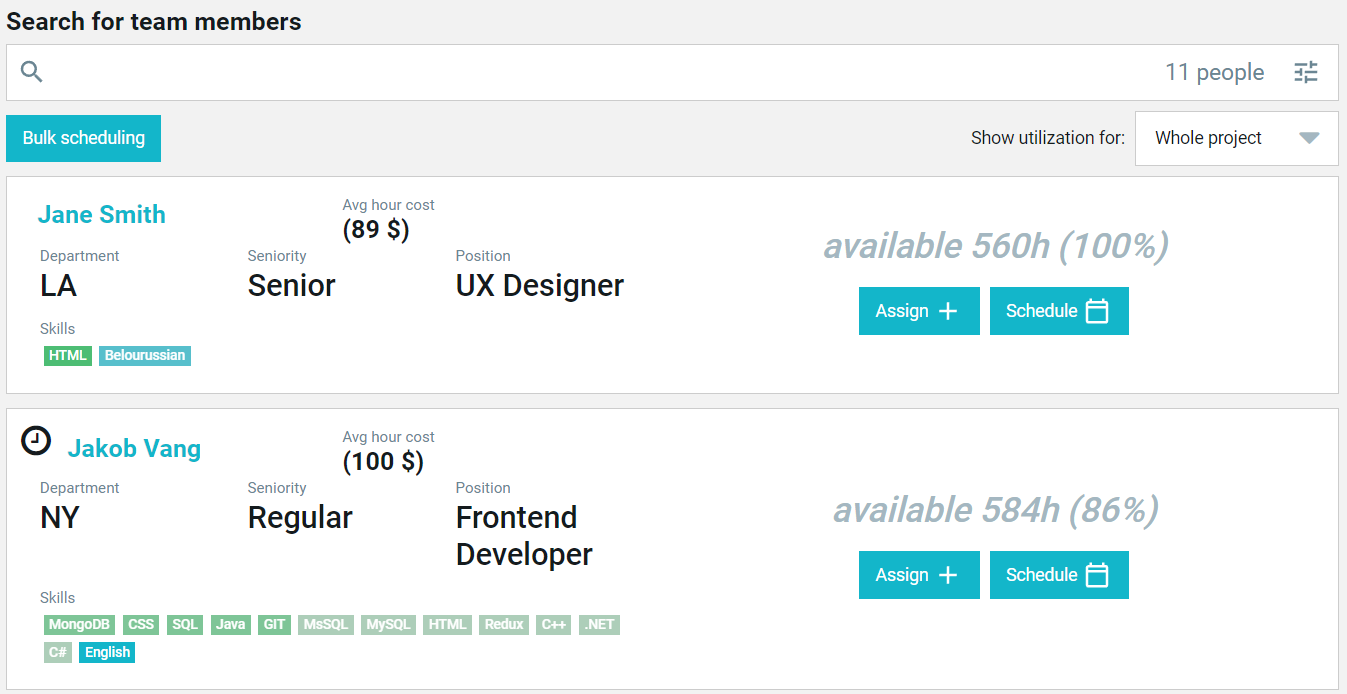
When the amount of work needed to complete a phase of the project is already known, resource planning can begin. In Primetric, resources can be assigned to the project in a dedicated search engine which helps capacity managers sort specialists by their skills and assign them to different phases of the projects - all while taking into account their availability.
Strategies for capacity management
Lag strategy
Companies using lag strategy are not looking far into the future. In fact, such businesses boost their capacity only when they already experience a sudden rise in demand for their products and services.
In other words, in lag capacity management strategy companies need facts and numbers, not predictions, to react and increase their capacity.
While this strategy may sound risky, it may be beneficial for companies which do not expect sudden spikes in demand. In such a case, they can delay large investments while minimizing the inventory - and, at the same time, costs.
However, the lag strategy also has its downsides. When used incorrectly, it may be a cause of overworking for the employees. It can also result in large delays when met with a rising number of orders and projects.
Lead strategy
Companies using lead strategy are usually very optimistic about their future. That is because they expect an increase in demand and prepare for it before it happens - and that is the main assumption of the strategy.
Unsurprisingly, the lead strategy is one of the most popular in the IT industry due to its rapid growth. It is also highly valued by the customers who can expect their project to be completed on time thanks to such an approach. As a result, companies often use lead strategy as a competitive advantage.
On the other hand, this advantage can sometimes turn into a nightmare. Whenever the demand falls or remains the same, companies using lead strategy are left with dozens of employees on the bench - and thousands of dollars running down the drain. Such proactive capacity management strategies should, therefore, be used carefully.
Match strategy
Match strategy combines lead and lag strategies to create a reasonable balance. In this approach, the capacity plan is performed frequently to closely monitor the situation and react to it in a flexible manner. As a result, the company can predict its closest future and prepare for it accordingly.
This strategy, in contrast to the ones I mentioned earlier, offers a variety of advantages. Flexibility, minimized risks and ability to scale are just a few of them.
However, while the positive side of match strategy may seem convincing, you should also keep in mind that it may not be enough on a dynamically growing market!
Adjustment strategy
Adjustment strategy is another proposition for the companies that want to base their operations on actual data. In this approach, businesses plan their capacity based on historical data gathered from different sources in the organization.
This strategy is particularly beneficial for companies with demand varying throughout the year. It may serve as a precise source of information - as long as the data is gathered with attention to detail.
Unfortunately, such an approach requires a number of additional tools. Without them, acquired prognosis would be inaccurate and misleading. As a result, such capacity management may be a source of additional and often unwanted costs.
.png)
Capacity management process: how to do that?
Capacity modeling from scratch
First time dealing with operations management? I have no doubts - it may sound like a scary and tricky task. Fortunately, when began with extensive research, capacity modeling can be not only useful, but also a simple operation.
Regardless of the industry you plan a capacity for, at first you should gather all the information you may need to determine each of three types of capacity mentioned above in this text.
As a result, your list of resources should include:
- Information on the product - business requirements, materials, necessary technologies, features, qualities and all the other characteristics related to the product itself.
- Information on the employees - number of specialists required to complete the process, their type of employment, availability, planned absences, skills, experience, etc.
- Information on the tools - available software and platforms, as well as the tools that need to be bought for this project only.
While the list may seem short, gathering the information will probably be the most time-consuming part of the service capacity management. That’s because it is crucial for all the consecutive steps of the operation - any mistakes on the list will result in incorrect capacity plan in the future!
Capacity management step by step
1. Start with demand planning process. Analyze the scope of the project and determine what skills and specialists you will need to succeed. Then compare them with your company's capacity, avoid capacity issues and make necessary decisions.
There are many ways to determine the demand for a given project. To do that successfully, you can:
- count the number of hours needed to complete the project or its phase,
- determine the number of FTEs for particular specializations,
- combine both of these methods by dividing the projects into high-level phases and determine the number of FTEs for each phase.
Example:
The Best Company wants to start a new project. The project was divided into a few phases:
- MVP
- Backend
- Frontend
- Tests
- Maintenance.
Each phase requires different specialists - therefore, their demand and capacity should be calculated separately.
The initial analysis have shown that the first phase of the project requires:
- a project manager with 160 hours available,
- a scrum master with 160 hours available,
- 2 UX designers with 80 hours available each in the first phase of the project (160 hours in total) ,
- 4 engineers with 160 hours available each (640 hours in total),
- 2 testers with 160 hours available each (320 hours in total).
As we can see from the list above, the first phase of the project is estimated to take 1440 hours to complete - and this value is the capacity of our project.
Further on, the same information has to be calculated for each phase of the project. The results of these calculations can later be added to provide you with an estimated time needed to complete the entire project.
2. Verify the resource utilization. Some of your employees may be preoccupied with other projects, while others may decide they do not want to work for you anymore (and others may take their place). Use the information on their current doings to check whether you need to hire some additional specialists to support a given project.
To come up with reliable conclusions, calculate the utilization with our guide. If you have a resource management tool, such as Primetric, you can use an advanced report to see the current status of resource utilization in your company.
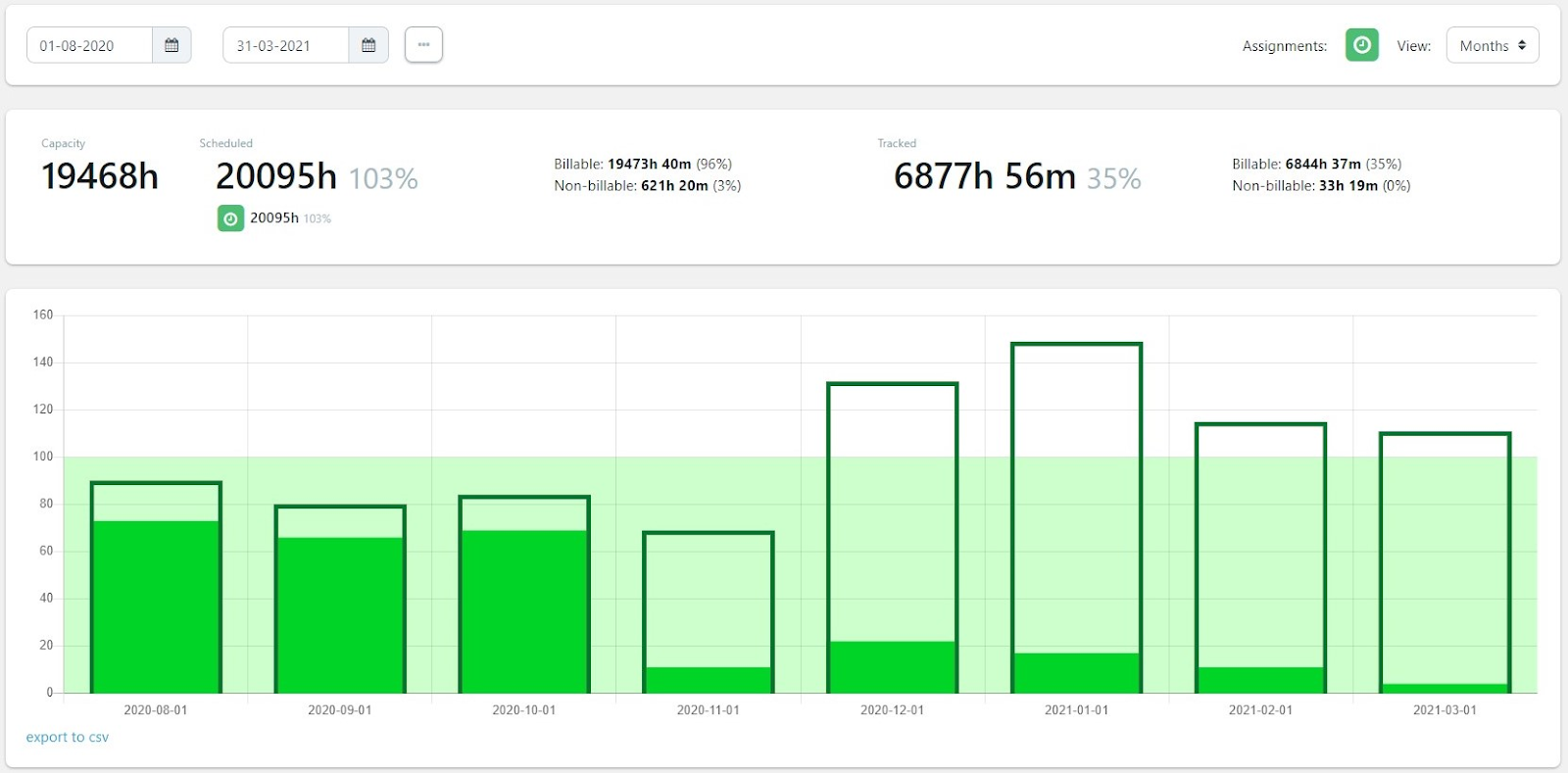
3. Calculate available capacity of employees necessary to complete the project. Include holidays, and other planned events and absences in the number of working hours for a given period.
To get an accurate result, use the formula:
Total capacity = number of working days * number of working hours * number of employees
Or use resource management tools to provide you with the information:
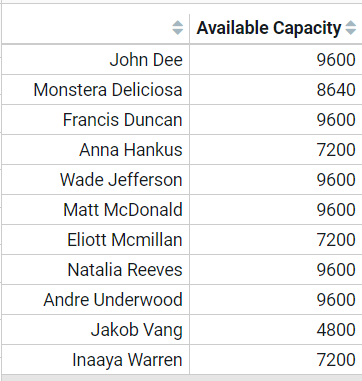
Example:
The Best Company already knows what resources it needs. On paper, it should only take one month to complete the project, as it requires max.160 hours from each employee. However, when The Best Company managers look at the calendar, they realize they are in trouble. That is because:
- The project manager will be on a planned sick leave due to a surgery. He will be absent in the first week of the month.
- The newly employed Scrum master is not yet with us - he will join the team at the beginning of the 4th week of the month.
- One of the testers will enjoy his two-weeks-long vacation by the end of the month.
- There is a public holiday scheduled for the second week of the month.
At this point, The Best Company also realized that it should take into consideration the number of hours its employees really spend working. According to the data the company gathered, the average working day equals 7 hours of project-related work. That value should also be taken into account while planning the capacity!
But how to calculate the capacity of the employees in that case?
Calculating the available capacity: basic example
Let’s start with the simplest examples: the employees that will only be absent during public holidays. For 7 employees (4 engineers, 1 tester and 2 UX designers) that will be the only extra day off that month.
5 employees (4 engineers and 1 tester) were supposed to work 160 hours that month. However, with a public holiday in the calendar, their capacity changes - to be exact, we need to deduct 8 hours from it.
160 - 8 = 152 hours of available capacity.
However, these specialists only spend 7 hours a day working on the project. Assuming that the month we are discussing has 19 working days and 1 public holiday, their capacity needs to be reduced by another 19 hours they lose to other activities every day.
152 - 19 = 133 hours = 1 employee’s billable capacity.
As stated above, the project requires 160 hours per employee to be completed. Therefore, it definitely won’t be finished this month!
Calculating the available capacity for half-time workers
We already know how many days full-time workers will spend working on the project. Now we need to calculate the capacity for employees that are just needed in the project for 80 hours - 2 UX designers.
As I pointed out before, they, too, will enjoy a public holiday, as their skills are necessary in the first phase of the project. As a result, their capacity drops by 8 hours.
80 - 8 = 72 = available capacity
Once again, we also have to take into account the time UX designers spend on their other duties. Just like in the example above, they lose 1 hour every day - but they will only work in this project for 10 full days, as they are half-time employees. They will also enjoy their public holiday, which is already included in the equation. As a result, we need to deduct another 9 hours from their existing capacity.
72 - 9 = 61 hours = UX designers’ billable capacity
As we can see from this example, UX designers will not finish their part of work in just 2 weeks - they will need another 3 days to complete the tasks that were scheduled to take 80 hours.
Calculating the available capacity for new and leaving employees
The IT industry is a very dynamic one. Consequently, companies such as The Best Company should expect the new workers to arrive at any time - and they also have to bear in mind that they can leave at any moment.
In the case of the latest project planned by The Best Company, the Scrum master is going to become a part of the company three weeks after the project was initially estimated to launch. As a result, his available capacity is drastically shrinking by 75%!
160 : 4 = 40 hours of available capacity.
Just like in the previous example, he will also spend less than that working. The Best Company has to deduct another 5 hours from this result because its employees can only work on this project for 7 hours a day. Therefore, the real billable capacity for the Scrum master is 35 hours in the last week of the month.
Calculating the available capacity in case of absences
Unfortunately for The Best Company, two of its employees are going to be absent really soon.
First, the project manager will be absent in the first week of work due to a planned surgery. According to the calendar, he should be working 160 hours this month. Still, he won’t be there for 40 hours - and that will have a serious impact on his capacity. To add to that, he will also have a day off during a public holiday. Therefore, his available capacity is:
160 - 40 - 8 = 112 hours
Then, he still won’t be able to work 8 hours a day, as this is our general assumption for all the employees. Therefore, his capacity is reduced by ⅛ - and the project manager is left with only 98 hours of billable capacity.
Last, but not least, one of two testers is leaving for a two-week long holiday. As a result of his voyage, his capacity drops by half. The lucky tester will also enjoy an additional day off during public holidays. Taking all these details into account, his available capacity is:
160 : 2 - 8 = 72 hours.
We have to keep in mind that his capacity has to be reduced by ⅛ once again - as we established before, the tester won’t be working full 8 hours a day. As a result, his maximum capacity is 63 hours.
For more information, read our guide for capacity calculation, as well as the information on resource utilization in your company. Alternatively, you can use Primetric to simplify this process with our resource planning tool.
4. Make decisions with capacity in mind. Service capacity management only has one goal: to ensure that the company has enough resources to complete orders or projects on time. Based on the analysis we performed in the example above, you can clearly see whether your company has the employees necessary to complete a given project. The information will help you make critical decisions.

In Primetric, the user's capacity is calculated using the data on his absences, contracts and other personal information. Then, the information is gathered in our search engine which helps managers find available specialists with the skills they need.
Example:
We know the exact capacity of people The Best Company intended to involve in their latest project. Based on the information, we can:
- change the starting date of the project, as the project manager and Scrum master will be absent at the beginning of the month,
- organize some replacements for employees that won’t be available to participate in the project to the full extend,
- decide whether new people are to be hired for the project, i.e. in case of a tester that’s going to be away for half of its duration,
- predict the need for overtimes caused by absences,
- estimate when the project will be finished.
4. Track progress. Use time tracking tools to monitor your specialists’ work and determine whether your estimates need to be adjusted. Adapt to the current circumstances and edit your project to meet your goals.
How can your company benefit from capacity plan?
Although capacity management may seem like a process meant for C-level management, it is also valuable for all the other specialists in your organization. In fact, various departments can benefit from it in a number of ways.
COO can use operations capacity management to:
- see the utilization rates within the company and react to any problems related to it;
- manage project effectively and introduce changes whenever necessary,
- discover the dependencies and connections between teams, operations and technologies and compare them to the projects to improve the pace of their execution. As a result, with capacity management COO can help his company scale faster than ever before,
- improve the communication between managers and shape their work without dozens of unnecessary meetings.
- detect potential costs caused by employing people not assigned to any project.
For PMO, capacity management shows:
- whether the processes are managed fluently and with no major issues,
- projects that may be delayed and, consequently, may result in lost profits,
- monitor the use of resources in real time.
Last but not least, CEO can use the conclusions from capacity management to:
- monitor major problems with delays, pauses and other issues that may affect the condition of the company,
- control his managers’ decisions and efficiency,
- see both the opportunities for growth and the issues that may be troubling for the company in the future.
With capacity management practice, sales department can:
- find out whether they have the resources necessary for a tentative project,
- check what specialists are available and find a new project for them.
On the other hand, capacity management heeps recruitment department to:
- find overworked employees and react to their situation,
- decide whether the company needs to hire new specialists,
- see what skills and abilities are necessary for the company to grow.
Best practices for capacity management
In the end, capacity management is not only about following a few steps. Just like in every other operation performed with dozens of other people, capacity planning also requires some universal practices that help this strategy get the message across. Those include:
- Constant two-way communication. Both planning and execution of each and every project depend on the transparency in the company. With no accurate data at hand, capacity planning may not be as reliable and effective as initially intended.
- Risk assessment. Projects executed by dozens of different people are prone to unforeseen problems caused by human factors. By taking it into account, you can predict the majority of issues and include them in your capacity plan.
- Shorter workday - at least on paper. There is not a specialist in the world capable of working 8 hours per day. Even the most productive people are distracted by meetings, e-mails, and, of course, well-deserved meals. As a result, in operations capacity management you should assume that you have less than 8 hours a day at your disposal.
- Adjusting to human resources. Your projects depend on your employees. Do not treat them like machines or materials; their well-being and happiness are as important for your project as the software itself. Adapt your approach to their needs to achieve the best results.
- Innovative capacity management tools. Planning doesn’t have to be done on thousands of papers or spreadsheets. Today, companies such as yours can rely on innovative tools that can do the majority of the work for them - and do the rest in just a few clicks. Hint: Primetric is one of such tools ;)
- Approval workflow. All the crucial documents and decisions should be shared with key managers and employees to ensure that all decisions are made unanimously. It also improves transparency and awareness of all the changes.
- Alerts for unplanned events. Unexpected sick leaves and other unforeseen obstacles should be visible in systems or spreadsheets a company uses for resource management. Such alerts allow the managers to make, change and adapt their decisions without keeping all the current changes in mind.
- Weekly / Monthly meetings. Not everything can be done in tools. Therefore, weekly and monthly meetings are a must. They are especially valuable when a company needs to reconsider and reshape its plans and make on-the-spot decisions in a dynamic environment. Still, on a daily basis, they can be used to analyze resource capacity and plans for the future.
Want to know more about good practices you can use for proactive capacity management? You’ve come to the right place - our customers have already done it successfully! Take a closer look at our case study created in cooperation with Monterail and see how they approached the process.
Calculating capacity: commom mistakes
On the other hand, while planning resource capacity for your company you should avoid:
- Being overconfident in your plans. Projects with too optimistic - and often unrealistic - assumptions are prone to delays and other issues. Assess the risk while keeping in mind possible issues to avoid spreading dissatisfaction amongst your customers and your employees.
- Disregarding people’s skills and ambitions. Mismatched specialists will do more harm than good to any project they may get involved in. The same thing applies to employees who wish to grow in different fields than they are working on. Such a situation can be damaging to both projects and turnover rates!
- Overestimating capacity. Christmas is coming and you forgot to include it in the schedule? Holiday season is upon us and you are left with no specialists in the office? Those are common reasons for projects to get delayed! Take them into consideration before you set the deadlines for your projects.
- Lack of workflow. Planning and implementation of operations capacity management are two very different things. Without proper workflow, the decision will remain just a few words on a piece of paper.
- Lack of demand planning. No company can successfully plan a project without resources - and demand planning is all about them. Omitting this phase can result in numerous open positions, swollen benches and, ultimately, enormous delays and losses.
- Ignoring the historical data. Tracked time can be used for something more than calculating salaries. By analyzing the historical data on hours worked, you can spot inconsistencies and opportunities and improve your estimations in the future.
Capacity planning may sound complicated - but it is worth it!
Capacity management involves a number of factors that may look very complicated at the first sight. Fortunately, it is just a first impression - the further you go, the easier the capacity planning becomes.
The principles are the same for all the cases, contracts and types of absences. Therefore, if you got a taste of these calculations with our examples, you should have no troubles estimating capacity in other, more complex cases, such as long-term absences, maternity leaves and sudden change of plans in the projects.
To add to that, your calculations will have a direct and positive impact on your company’s finances.
With capacity planning, you can:
- successfully plan your projects without interfering with the existing ones,
- prepare for all the unexpected scenarios and react to them in the real time,
- realistically estimate the date of completion for all the projects,
- find and fill in the gaps benched employees have by finding them additional project,
- maximize your revenues by using your workforce to the fullest.
Also keep in mind that you generally do not have to complete all of these calculations manually. Resource management tools, such as Primetric, can perform these calculations with just the basic data entered into the system. With such tools, capacity planning can not only simplify your work, but also save your time.
Improve capacity calculations in a few simple steps
Are you getting a feeling that all of those things are too complicated to be done in a spreadsheet? Is it time-consuming? Or maybe it's just an exhausting and repetitive procedure?
We agree with you - that is why we created Primetric.
With Primetric, you can see all your resources along with their availability. Thanks to that, you can accurately plan your future operations while improving the morale of your specialists.
How?
Let us show you - book a demo with Primetric and reshape capacity planning processes in your company.